In-plant printing experts agree that production flexibility is increasing in importance and inkjet can help operations to adapt. In this article, sponsored by Kyocera, Lois Ritarossi interviews Christopher Donlon of the IPMA and Mark Fallon of the Berkshire Company and discusses the accessibility of inkjet printing for in-plant printing operations of all sizes.
Thought leaders see numerous changes impacting in-plant print and mail operations (in-plants) and their evaluation of new equipment and software. Challenges with labor, hiring, and training new staff to run older equipment, are leading more in-plants to consider inkjet.
I recently discussed the challenges faced by in-plants with Christopher Donlon, president of the In-Plant Printing and Mailing Association (IPMA) and Mark Fallon, president and CEO of The Berkshire Company. Christopher Donlon is the senior manager of digital and print production at the in-planting printing operation for Kohler Company in addition to his leadership of IPMA. Mark Fallon is a consultant who assists in-plants across many verticals with operational efficiency, acquiring new technology and providing value to their organizations.
Christopher Donlon, President, In-Plant Printing & Mailing Assoc. (left) and Mark Fallon, President & CEO, The Berkshire Company.
In terms of the post-COVID production print landscape, Fallon immediately pointed to the importance of flexibility. While print operations in the past focused predominantly on long-run jobs, they now include a greater volume of shorter, more personalized tasks. Special requests from their internal business units and marketing departments are becoming more common. In-plant managers, as a result, are having to adapt, and quickly.
The Migration to Inkjet
The pandemic stretched out equipment lease cycles, with uncertainty persisting through 2022. Companies are finally moving forward with new acquisitions. Fallon told me that two of his current in-plant clients cited cost-efficiency and color requirements as drivers of their 2023 RFPs for the acquisition of inkjet. “Improved inkjet and digital output provide competitive alternatives to bypass traditional offset when color is needed,” said Fallon. “Older toner devices, while less expensive than in the past, are still more expensive than inkjet.”
In-plant managers shared their inkjet success stories at the recent Inkjet Summit and IPMA Annual Conference. Donlon said IPMA members are investing in inkjet because the quality is comparable to offset. Other factors in favor of inkjet installations are the ease of training new operators and ongoing maintenance, which can be done without the advanced skills needed for offset presses or maintenance requirements of digital toner devices. Inkjet delivers significant improvements in uptime over digital toner and requires less onsite maintenance.
Fallon said requirements for space and HVAC also have a major bearing on capital investments. Space includes requirements for the delivery of components in crates as well as room for operating the press in production. Sheetfed digital presses, particularly B3 format presses, tend to be more space-effective than rollfed or larger format (B2 or B1) equipment, although there are B3 inkjet devices on the market with an overall footprint larger than a B2 press.
Donlon stated that in-plant managers are comparing the cost of inkjet to what they currently spend on lease payments, clicks, and supplies as they calculate the ROI for new investments. The cost of entry for inkjet has decreased in the last few years with more sheetfed inkjet models on the market as original equipment manufacturers (OEMs) respond to the industry’s labor challenges. Tenured, highly skilled operators are retiring, and open positions are being filled with less experienced workers. Solutions that require less training and technical expertise are critical, along with improved automation for greater workflow efficiency and finishing.
When it comes to evaluating the operating costs for different technologies, inkjet has turned the industry on its head, with some OEMs removing click charges from the equation. Fallon notes that the customers he works with are looking at the entire cost from receipt of order to finished pieces in order to compare the labor, variable, and fixed costs for each print solution.
In-plant managers have learned to align themselves with their business units and their marketing departments to demonstrate ROI and positive impact on their organizations. For the healthcare and financial services verticals, for example, inkjet technology has enabled in-plants to support marketing needs for customization and personalization while maintaining in-house jobs that were previously outsourced. Many K–12 school districts as well as colleges and universities have installed inkjet so that they can deliver color at their previous cost of black-and-white toner printing. It’s a win for the students, teachers, and in-plant print operations.
The Small-Footprint, High-Impact In-Plant Solution from Kyocera
An industry with a long history and proud heritage, production print is now gearing up for an exciting new chapter thanks to the emergence of dynamic technologies that have been tailored to the needs of modern business.
With the TASKalfa Pro 15000c, for example, Kyocera has found the sweet spot between affordability, media versatility, and the impressive quality and consistency offered by its industry-renowned inkjet printheads. It is precisely this blend that has a lot of in-plant managers thinking differently about where they might enter with production inkjet or how to replace existing toner devices.
The TASKalfa Pro 15000c was designed for ease of operation and simplified maintenance. With a standard configuration that measures 38 x 29 x 48 in. (or 965 mm × 740 mm × 1220 mm.) in length, depth and height, the footprint provides flexibility to fit in many environments. Key features include:
- Low capital cost commensurate with 100 ppm toner devices.
- Ease of operation, including an intuitive touchscreen interface and workflow tools that support both color management and media profiling.
- Supports a wide range of uncoated offset and inkjet-treated stocks.
- Flexible configurations for different volume levels and finishing options.
- Full-color production at a consistent speed, meeting G7 color standards on uncoated media.
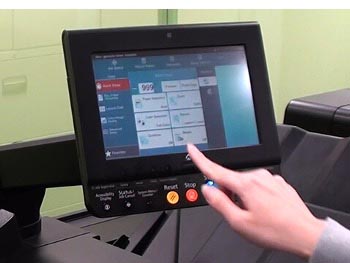
Kyocera TASKalfa Pro 15000c operator touch screen interface. Source: Kyocera
The TASKalfa Pro 15000c is simpler to operate and maintain than toner devices. This is due, in part, to the fact that inkjet has fewer moving parts that wear down and need to be replaced than toner, but also due to what Kyocera describes as exceptionally long-lasting and high-reliability parts. With increased uptime and fewer maintenance tasks, inkjet operators can focus on simple tasks such as monitoring jobs and loading and unloading stock.
As in-plants take on shorter runs, ad hoc, and customized print jobs, the TASKalfa Pro 15000c provides flexibility to support a wide variety of print applications. The press runs at 150 ipm consistently across all supported media in simplex or duplex modes. The printer runs standard paper sizes up to 13 x 19.2 in. with an optional banner tray for extra-long paper sizes up to 48 in. It also supports feeding of irregular surfaces such as embossed paper and tabbed media. Marketing teams prize specialized media for eye-catching designs and tactile engagement with print. The press can be configured with up to eight input paper feeders (six standard) delivering a capacity of over 14,000 sheets (4,150 standard). This extended capacity supports larger jobs and the ability to combine smaller jobs for greater productivity.
While the speed and simplicity of the TASKalfa Pro 15000c can increase productivity per shift, its low running cost is also important for in-plants where cost chargebacks rather than market pricing are the norm. Power consumption is just one of the many cost considerations where the device shines. The TASKalfa Pro 15000c runs on standard 100-volt power and has no special requirements for HVAC. This eliminates any need for costly additional site work prior to installation. The low average energy usage of just 3.8 KwH keeps minimizes power contribution to overhead expenses.
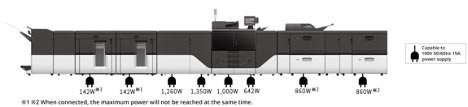
Kyocera TASKalfa Pro 15000c Power Configuration. Source: Kyocera
Since many in-plant operations also provide departmental copying and reprographic services, it is notable that the TASKalfa Pro 15000c includes high-quality photocopying and scanning functions and can be used as a high-speed, multifunction printer, when not being used for production printing, to drive further cost efficiency through increased volume. This combination makes inkjet accessible to even small in-plant operations for which full-color inkjet had been out of reach. Donlon notes, “Like many in-plant managers, I never thought I had the volume of work to justify an inkjet investment. I have a new perspective after seeing the newer cut-sheet inkjet printers which offer automation, ease of use, and reduced labor cost.”
Many successful in-plants have already adopted high-speed inkjet to provide high-quality, cost-effective printing services to increasingly demanding internal customers. Those who have not yet invested are often smaller operations using toner, or in-plants focused on producing forms and collateral using traditional offset presses. But we have entered a new age of production print, and the Kyocera TASKalfa Pro 15000c provides an attractive option to replace toner or complement offset presses and do more for customers.